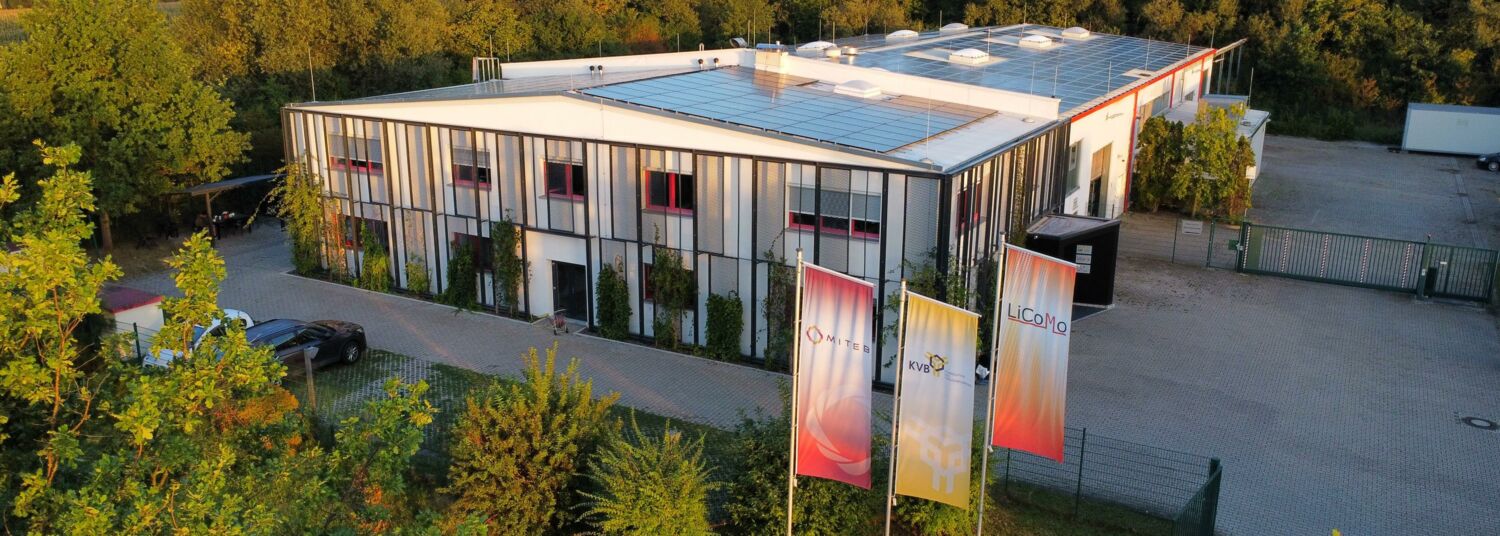
Effiziente Recyclingprozesse zur Verwertung anfallender Prepreg-Reste aus CFK
Christoph Albani, Jenny Graichen
Durch den steigenden Einsatz von CFK-Bauteilen gewinnt deren Recycling zunehmend an Bedeutung. Prognosen gehen davon aus, dass im Jahre 2023 alleine 197.000 t CFK verarbeitet werden [Quelle: Composites Marktbericht 2019]. Damit steigen auch die Abfallmengen bei der Herstellung der Bauteile drastisch an. Derzeit werden allerdings nur 5 – 10 % der anfallenden Abfallmengen einem Recycling zugeführt [Quelle: Fachtagung Composites Recycling & LCA 2021]. Daher gilt es effiziente Recyclingprozesse zu entwickeln, um die im Stand der Technik übliche, umweltbelastende Deponierung oder energetische Verwertung langfristig zu vermeiden. Zudem fordert die Politik zunehmend einen nachhaltigen Umgang mit derartigen Ressourcen.
Im Rahmen eines Forschungsvorhabens beschäftigen sich Wissenschaftler am Institut für Konstruktion und Verbundbauweisen gemeinnützige GmbH (kurz: KVB) mit der effizienten Verwertung anfallender Produktionsreste beim Zuschnitt von duroplastischen Prepregs. Sowohl in der Luftfahrt als auch im Automobilbau fallen bis zu 35% Verschnitt beim Zuschnitt dieser vorimprägnierten, bahnenförmigen Prepreghalbzeuge an. Der Anteil der teuren Ausgangsmaterialien wird bislang üblicherweise als Sondermüll entsorgt. Die Wissenschaftler am KVB wählen hingegen einen anderen Ansatz. Dabei werden die Verschnittreste aus dem Carbon-Gewebeprepreg in Faserschnipsel definierter Abmessungen zerkleinert. Dies hat gegenüber bisherigen Recyclingprozessen wie der Pyrolyse den Vorteil, dass energetisch aufwändige Prozessschritte zur Trennung von Matrix und Faser vollständig vermieden werden können. Durch einen nachgelagerten Prozessschritt können diese imprägnierten Faserschnipsel anschließend zu Endlosbahnen, plattenförmigen Halbzeugen (Patches) oder direkt zu komplexen, bauteilnahen Zuschnittgeometrien verarbeitet werden. Letzteres kann weitere Kosteneinsparpotentiale zur Folge haben.
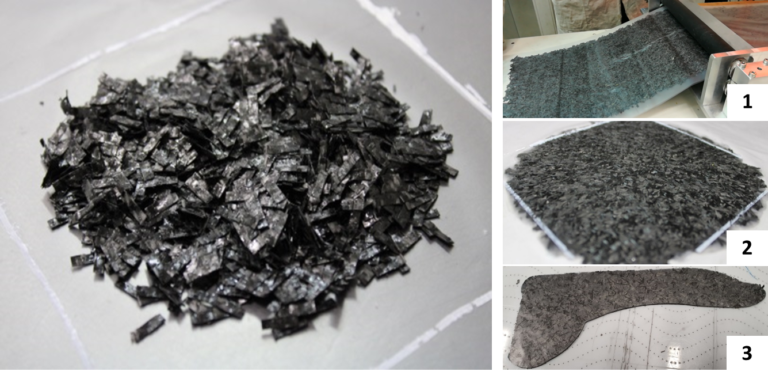
Verfahrensbedingt resultieren bei den rSMC-Halbzeugen bis zu vierfach höhere Flächengewichte, wodurch sich in der Folge weitere Kosteneinsparpotentiale bei Zuschnitt- und Laminierprozessen ergeben. Zudem geht mit den kurzen Faserlängen von wenigen Millimetern ein verbessertes Drapierverhalten einher, wodurch auch komplexeste Bauteilgeometrien ohne jegliche Falten- oder Fehlstellenausbildung abgeformt werden können. Bauteile aus rSMC weisen darüber hinaus durch ihre wirre Faserverteilung quasiisotrope Eigenschaften auf. In Sachen Porengehalt (< 1%), Oberflächenrauigkeiten und Glanzgraden stehen sie den Bauteilen aus Primär-Gewebeprepregs zudem in nichts nach. Ein weiterer wesentlicher Vorteil des rSMC-Materials besteht in der Kompatibilität zum ursprünglichen Gewebe-Prepreg. Damit sind die gleichen Fertigungsprozesse anwendbar und auch Kombinationen beider Materialien grundsätzlich möglich. So ist der Einsatz als Rissstopperschicht ebenso denkbar wie die Verwendung als Bagging- oder Fülllage in Bauteilen auf Basis von Gewebeprepregs. Aber auch komplette Bauteile mit „Sichtcarbonoptik“ aus rSMC sind denkbar.
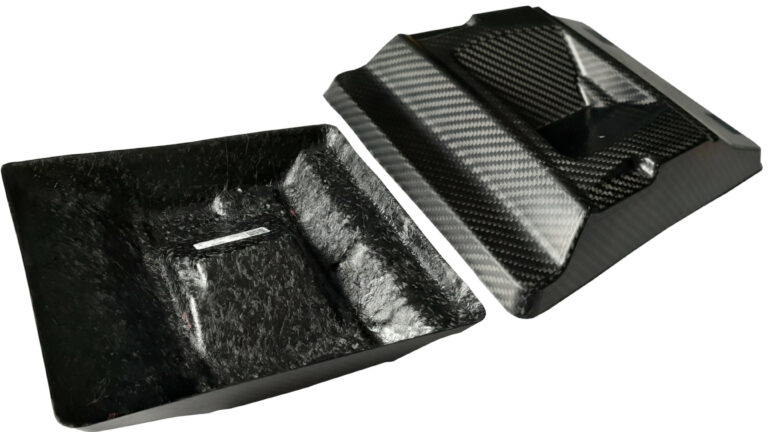
Die Bewertung der Wirtschaftlichkeit des entwickelten Prozesses lieferte Kosteneinsparungen von bis zu 70% gegenüber dem Ausgangsmaterial bei einer Gesamtrecyclingfähigkeit von bis zu 85 %. Damit leistet der Ansatz einen wichtigen Beitrag zur Abfallreduktion für diesen Sektor.